導入事例
岡野バルブ製造様5軸MCとSolidCAMで劇的な生産時間の短縮に成功
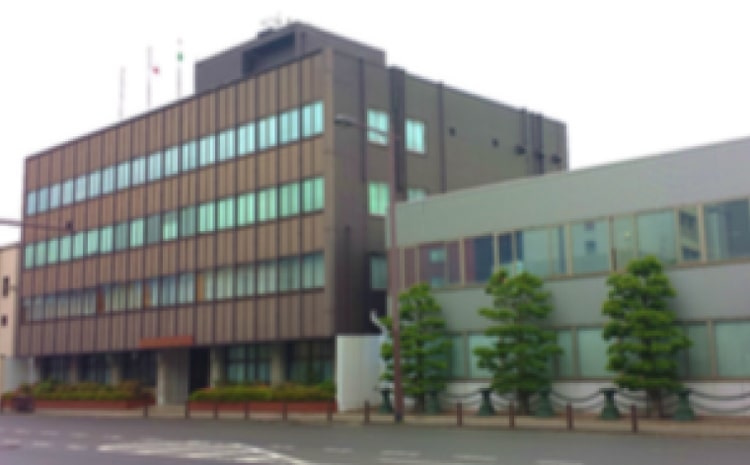
- 社名
- 岡野バルブ製造株式会社
- 創業
- 1926年(大正15年)
- 本社
- 福岡県北九州市門司区中町1-14
- 上場
- 東京第2部・福岡
- 社員
- 274名(平成25年11月時点)
- 製品
- 各種工業用弁装置の製造
- 認定
- ISO9001・ISO14001他
日本のエネルギー基盤を支える「ものづくり」と5軸MC
福岡県北九州市にある岡野バルブ製造株式会社様は、主に火力発電所や原子力発電所で使われる耐高温高圧のバルブ装置を製造されていらっしゃいます。過酷な使用条件に耐えるため、難削材に分類される特殊な合金を材料に用いることもあるそうですが、長年の実績に裏打ちされた同社の製品は、日本国内のみならず、海外でも評価が高く、米国や中国など海外にも輸出されています。
同社の切削加工は、旋盤38台、マシニングセンター4台、中ぐり盤5台他という台数に表されるように、旋削加工が中心でした。そのため、フライス系の生産効率向上は、これまであまり優先順位が高くなかったため、2008年(平成20年)に、初めて森精機(当時)の5軸マシニングセンタNMV5000を導入した際には、本当に使いこなせるのかと、現場の一部からは不安の声もあがったそうです。
CAMの選定 3つのポイント
当時5軸マシニングセンタ立ち上げのリーダーだった石田様(現:総務部)によると、CAM選定において3つのポイントがあったそうです。
- 同社設計CAD「SolidWorks」との連携性
- CAMの操作簡易性 (とくに同一形状・異寸法に対して)
- CAM販売会社のサポート体制・加工知識
複数候補との比較の中で、上記3つの合計ポイントが高かったのがSolidCAMを御導入頂いた理由とのことでした。
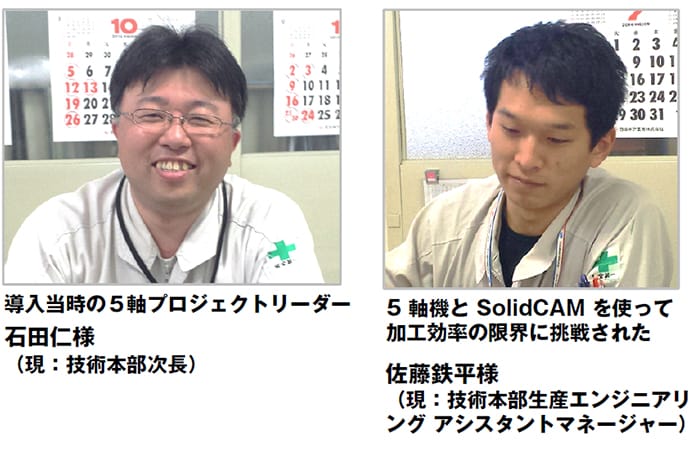
~加工ノウハウ「0ゼロ」からの5軸立ち上げ~教訓1:「5軸はCAD/CAMだけでは動かせない」
導入当初、5軸加工については、社内の誰にも聞くことができなかったため、試行錯誤の連続でご苦労されたとのことです。
中でも一番重要だったのは、干渉・衝突を避けるための「加工前のNCデータによるシミュレーション」と言うお声を石田課長補佐と現在のご担当者の佐藤主任の御両名より頂きました。同社は、アイコクアルファ社製のGコードシミュレーターである「G-Navi」を現在も御利用中です。
シミュレーターがないと、機械オペレータが現場に「つきっきり」で加工に立ち会わねばならず、現場効率が著しく低下するという現場の問題もさることながら、万一の事があった場合に、復旧費用以外に、 会社の信用問題(納期や精度など)に影響を与えるリスクの方が問題だとの見地から、導入したとのことでした。
~加工ノウハウ「0ゼロ」からの5軸立ち上げ~教訓2:「空圧VS油圧 5軸性能を最大限に引き出すのは?」
5軸加工のメリットである「ワン・チャッキングでの複数面の連続加工」を行なうためのワークの掴み方や、最適な工具の突き出し量の組み合わせを見つける試行錯誤の過程で、大きな壁にぶつかったのが直径80mmのフェイスミルによる加工。
それは固定5軸加工で、ワークにびびり(振動)が出て、機械側のクランプが緩んでしまうという問題でした。
機械メーカーからの助言を踏まえ、機械側のクランプの駆動を空圧から油圧に切り替えることでこの問題を解決した同社は、その後も機械性能を最大限に引き出すための取り組みを続け、導入当初は10~12時間かかっていた加工を、4~6時間まで短縮することができました。
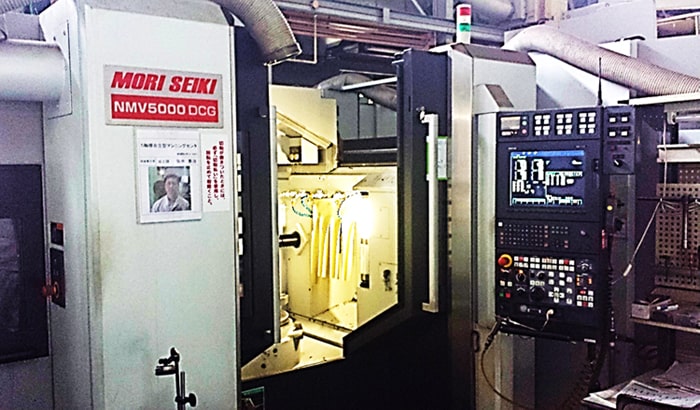
~加工ノウハウ「0ゼロ」からの5軸立ち上げ~教訓3:「時間短縮のために加工パスにも徹底的にこだわる」
その次に同社が着目したのが、加工時間を短くするための加工条件と加工パスでした。
鋭角コーナーでも送り速度が減速しないような滑らかな加工パスによって、それまで4~6時間かかっていた加工を1~2時間まで短縮しました。(SolidCAM HSMオプション)
更に、工具接触面積を一定角度に保つことで工具負荷を一定にするトロコイド状の加工パスで、 かつ、ワーク素材や工具突き出し量、刃数などの条件から自動計算される最適な加工条件によっ て、最終的には1時間以下に短縮することに成功しました。(SolidCAM i-Machiningオプション)
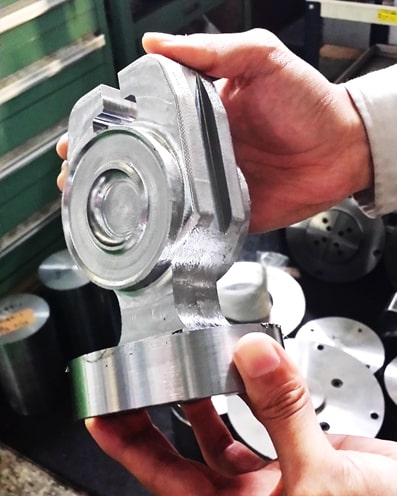
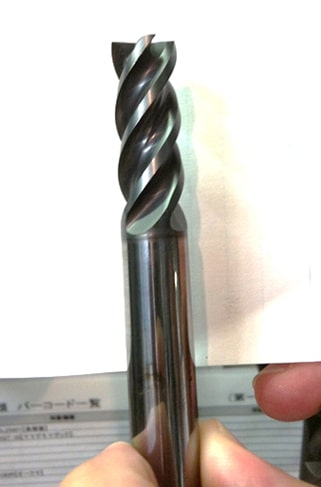
加工方法 | ![]() |
---|---|
工具 | 日立ツール 超硬エンドミル / φ12 / 4枚刃 |
ワーク | S25C |
加工条件 | 1回のZ切込み量 17mm / S3799 / F2375 |
加工時間 | ![]() |
~5軸MC導入のビフォー・アフター比較~「素材形成加工+1次加工」による「生産性向上+コストダウン」
5軸MCを導入した目的は、自社鋳造後に切削加工を行なうのではなく、丸棒などの市販鋼材の形状から直接、削り出す1次加工を行うことで、「小ロット短納期化」と「コスト削減」を同時に達成するためでした。
さまざまな挑戦を重ねたことで、ノウハウが蓄積され、フライス系の切削技術は飛躍的に高まったとのこと。今では「これも5軸MCで加工できないか?」と社内検討が広がり、導入当初は本当に使いものになるのか?と不安視されていたのが嘘のようだ、と石田課長補佐。
ワーク寸法や主軸回転数など機械側の制約もあるが、5軸MCで加工できるアイテムを増やしていきたいとのことでした。
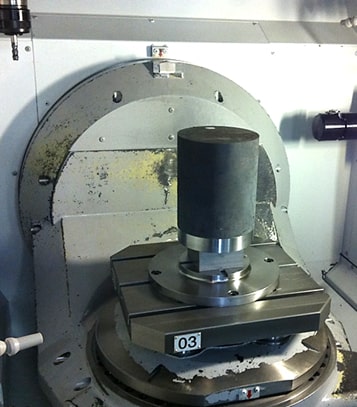
- 様々な木型が必要で、素材納期は平均約3週間(鋳鋼法案作成→木型作成・検査→鋳込み→処理→研磨・仕上→運搬)
- 鋳鋼欠陥の発生による工程停滞
- 夜間無人運転および複数個加工が出来ない
- 工程数が多く、段取り時間が多い
- 市販鋼材購入により鋳鋼費ゼロ、素材欠陥無し、素材納期短縮
- 5軸MC機に5パレットチャンジャー搭載により夜間無人運転/複数個加工が可能に
- 工程集約による段取り時間の減少
これからも世界をリードする日本のものづくりのために
経済産業省も注目する次世代のエネルギー技術「A-USC」(700℃超臨界圧発電システム)の実用化に向けた研究開発も行なっている佐藤主任に今後の抱負をお伺いしたところ、現在5軸MCに限定されている3次元CAD/CAMの活用範囲を、フライス系から旋削にまで広げ、製造部として会社の更なる生産効率の向上を図りたい、とのお言葉を頂きました。
岡野バルブ製造株式会社様の今後の益々のご発展をお祈りいたします。